Rotary Table
Rotary Table
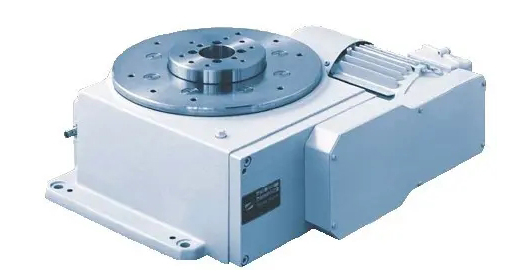
Rotary tables or rollers used to position work so that all welds can be made in the best position, for example flat or horizontal–vertical, present a number of hazards which have been overlooked in the past by welders. A safe working load, maximum work dimensions and allowable out of balance load should be established to avoid over-stressing the equipment. Where work is moved during welding, the return path for welding current must be considered; if a cable is used, will it coil up safely as work proceeds or will an assistant be needed to guide it? If a cable is not used the return current must not be allowed to pass via the bearings and damage them, but through a proper slip ring and brush, usually provided on equipment intended for this duty. Manipulators should be securely fastened to a sound foundation or a large unbalanced load may cause them to tip over suddenly during welding.
As with any motor-driven equipment, the welder should have ready access to an emergency stop button.
Where circular work such as drums or pipes is rotated on rolls, suitable precautions should be taken as required to detect and rectify any tendency for the work to creep along its axis of rotation. Work with holes in the outer diameter, or projections such as stub pipes, may foul rollers or fixed plant during rotation.
Particular care is needed to avoid starting with a safe piece of work, which is then built up to a weight or size exceeding the capabilities of the equipment in use.
Previous: Oil drilling
Next: Compact Hand Robot