Robotics
Robotics
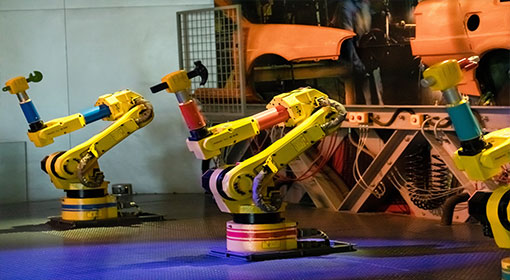
Robotics is an interdisciplinary branch of engineering and science that includes mechanical engineering, electronic engineering, information engineering, computer science, and others. Robotics deals with the design, construction, operation, and use of robots, as well as computer systems for their control, sensory feedback, and information processing.
These technologies are used to develop machines that can substitute for humans and replicate human actions. Robots can be used in many situations and for lots of purposes, but today many are used in dangerous environments (including bomb detection and deactivation), manufacturing processes, or where humans cannot survive (e.g. in space, under water, in high heat, and clean up and containment of hazardous materials and radiation). Robots can take on any form but some are made to resemble humans in appearance. This is said to help in the acceptance of a robot in certain replicative behaviors usually performed by people. Such robots attempt to replicate walking, lifting, speech, cognition, or any other human activity. Many of today's robots are inspired by nature, contributing to the field of bio-inspired robotics.
The concept of creating machines that can operate autonomously dates back to classical times, but research into the functionality and potential uses of robots did not grow substantially until the 20th century. Throughout history, it has been frequently assumed by various scholars, inventors, engineers, and technicians that robots will one day be able to mimic human behavior and manage tasks in a human-like fashion. Today, robotics is a rapidly growing field, as technological advances continue; researching, designing, and building new robots serve various practical purposes, whether domestically, commercially, or militarily. Many robots are built to do jobs that are hazardous to people, such as defusing bombs, finding survivors in unstable ruins, and exploring mines and shipwrecks. Robotics is also used in STEM (science, technology, engineering, and mathematics) as a teaching aid.
The advent of nanorobots, microscopic robots that can be injected into the human body, could revolutionize medicine and human health.
Robotics is a branch of engineering that involves the conception, design, manufacture, and operation of robots. This field overlaps with electronics, computer science, artificial intelligence, mechatronics, nanotechnology and bioengineering.
Robotics & Automation Bearings
The use of robotics and automation continues to grow more prevalent across industries, particularly in manufacturing, as companies are realizing the full potential of its ability to reduce costs, boost production and deliver greater efficiency and competitiveness.
Typical industrial robotic applications include welding, painting, assembly, product inspection and testing. As the technology has progressed, automation has demonstrated exponential improvements in endurance, speed and precision, with more sensitive applications in medical and other high-tech sectors becoming common.
With highly choreographed, programmed movement on two or more axes, bearings play a major role in the motion control aspect of this technology. The use of high-precision bearings are an integral consideration for those tasked with designing and maintaining these applications. Bearing life and performance demand that the correct type, material and lubrication are specified.
Single-row deep groove ball bearings, with sizes ranging from miniature to extra-large, are generally the go-to bearing choice for the majority of robotic and automation applications. Thin section bearings are often designed into robot arm joints due to their low mass, space-saving construction and high-speed capability.
Roller bearings are usually the first choice for heavy-duty requirements. Slewing rings are a common selection for the main rotation and associated lift equipment. Hybrid (ceramic balls with stainless steel rings) and full-ceramic bearings are an excellent alternative for operation in a vacuum or other inhospitable environments.
The hazardous environments to which robotic applications are often subjected demand proper contamination protection in order to prevent debris of all types, shapes and sizes from entering the bearing and causing irreparable damage or premature failure.
There are many bearing closure types available, each with their own set of advantages. Regardless of the style, closures extend bearing life by preventing contaminants from reaching critical surfaces inside the bearing and help retain lubricant in the bearing.
Metallic shields make no direct contact with the inner ring, which minimizes rotational torque and helps maximize operating speed. Molded rubber seals (typically made from trusted Buna-N material) make contact with the inner ring, which provides better protection in more contaminated environments compared to metal shields, but would also increase startup and running torque due to seal resistance.
Seals might also decrease maximum rotational speed against desired rpm level, which must be taken into consideration. Depending on the bearing type, combination style seals/shields may be available for extra protection.
With excellent resistance against exposure to certain chemicals, glass reinforced PTFE seals may be a preferred choice, as it also allows higher running speed and less torque resistance compared to rubber seals.
The operating environment, applied load and intended motion profile may also influence the selected bearing material. For harsh or corrosive environments, typical in medical, food service and chemical processing applications, 440C stainless steel is often specified for the rings and balls instead of standard hard chrome steel material.
Proper bearing lubrication is another important consideration in optimizing performance and extending the life of the bearing. For example, in food and beverage processing environments, strict regulatory guidelines often dictate the use of H1 food-grade lubricants – which typically have synthetic, hydrocarbon base oils with urea, polyurea or aluminum complex thickeners – due to the possibility of incidental contact.
The critical functions of the lubricant is to minimize frictional resistance and wear of the moving parts, which are (in the case of bearings) the balls or rollers and the ring raceways. A lubricant that is designed for specific operating conditions will provide a proper load-bearing, wear protective film. The ideal condition maintains separation of these frictional surfaces by this film. Moreover, the lubricant will allow for heat dissipation and overall bearing thermal stability. The proper lubricant selection will avoid rapid deterioration over time as well as offer protection against corrosion, moisture and contaminant ingress.
Bearing optimisation for robotic applications
The idea of personal robots assisting with the housework seems great, but we’re a long way away from the technology being effective and affordable enough to see uptake on a large scale. The precision and accuracy required for ‘consumer’ robots to become a reality is becoming increasingly possible thanks to research and development conducted in industrial automation, particularly in the last decade.
From production and packaging to surgical environments, robots are performing increasingly complex tasks, faster and with more precision than ever before. In operating theatres, for example, robots can perform complex surgeries with such repeatable accuracy that associated risk to the patient has dramatically fallen, while recovery time has increased.
Our relationship with industrial robots is also changing. On the factory floor, collaborative robots are breaking out of the cages that have traditionally confined them, to work in the open alongside people.
These developments have been made possible by advancements in motor, actuator and sensor technology as well as the all-important bearing. Hybrid chrome and steel bearings, ceramic bearings and slewing bearings are all common in robotic applications, but thin section bearings also have a key role to play, but these can be overlooked by engineers.
Low space requirement
Thin section bearings deliver higher speeds, improve efficiency, offer higher levels of design flexibility as well as reduce friction. And, because there is very little difference in size between the internal and external ring, they also reduce the weight and bulk of an application, making them an ideal choice for robotics, where both footprint and weight are premium items.
However, because they are so thin, particular attention should be paid to the roundness of the ring itself. If you take a thin section bearing without any lubricant and spin the inner ring, a light squeeze of the outer ring will stop the bearing in its tracks, thanks to the flex in the device.
As a result, the manufacturing process must be extremely precise to ensure the highest possible degree of roundness in both rings, as well as good noise levels in the bearing itself. This will normally call for fine grinding and machining, complimented by a very high level of quality in both the process and the raw materials. If the rings are not perfectly formed, even a minute discrepancy will stop the bearing running smoothly, producing excess noise.
These thin-section ball bearings can be supplied open, shielded or sealed in SAE52100 chrome steel or 440 grade stainless steel and are designed to withstand some radial loads as well as moderate thrust loads in both directions. Some of the smaller thin-section bearing sizes are also available with a fibreglass reinforced nylon high speed synthetic retainer.
Thin section lubrication
You should choose a low torque, free turning and low noise grease for a thin-section bearing, as an overly stiff grease won’t deliver the best results and could increase bearing torque to unacceptable levels.
A grease with a temperature range of -40 to 150°C would be most suitable as this reflects the variety of applications in which a robot is most likely to be used, from refrigeration to locations near a furnace. It’s also important to select a food grade grease if the robot is going to be used in food or beverage production or packaging.
The right grease choice will result in a free running bearing, which in turn will reduce the power consumption of the machine itself, as well as the long-term maintenance costs. It is also one of the factors that can contribute to the overall speed of the robot arm.
So, while humanoid robots may not be cleaning our homes, it does seem likely that their impact on industry will continue to increase apace.
Previous: Oil drilling
Next: crane loading platform