MONTON EXPERIENCE
MONTON is the leader of super precision ball bearings. Our goal is Solve problems for customers and prioritize
customer service at first.Monton have more than 30 years market-leading expertise in the design and manufacture
of super precision ball bearings. We can supply high precision bearings according to to the demands and requirem
-ents of our customers. We produce high quality bearings and offer full range tehcnical support.
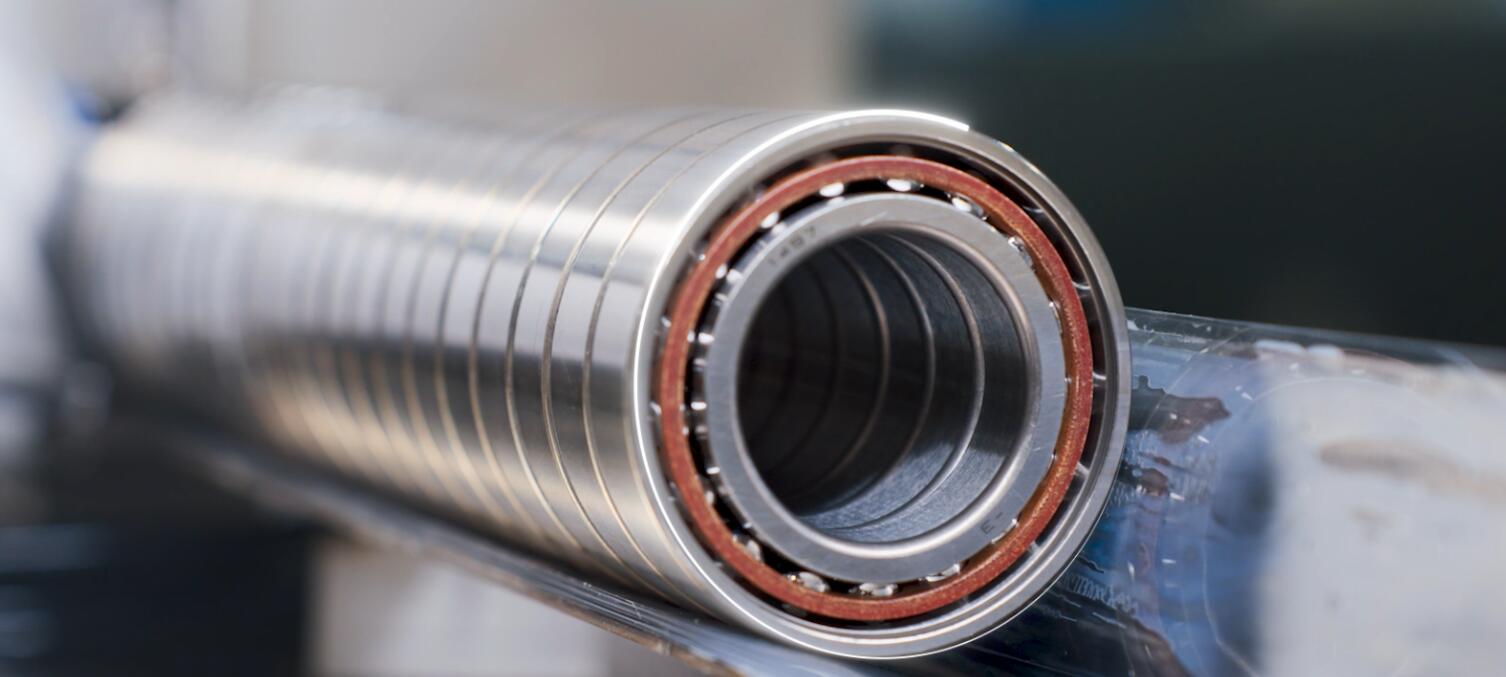
Our super precision ball bearings
Our mian high precision angular contact ball bearings product range from 3mm inner diameter up to 500mm outer
diameter. These bearings designed specially to reach long lifetime and suitable for the highest workingspeeds and
through optional high quality materials, extreme corrosion resistance.
We prepare most high precision bearing in stock and we can fully meet the demands of our customers at all times
and deliver product quickly.
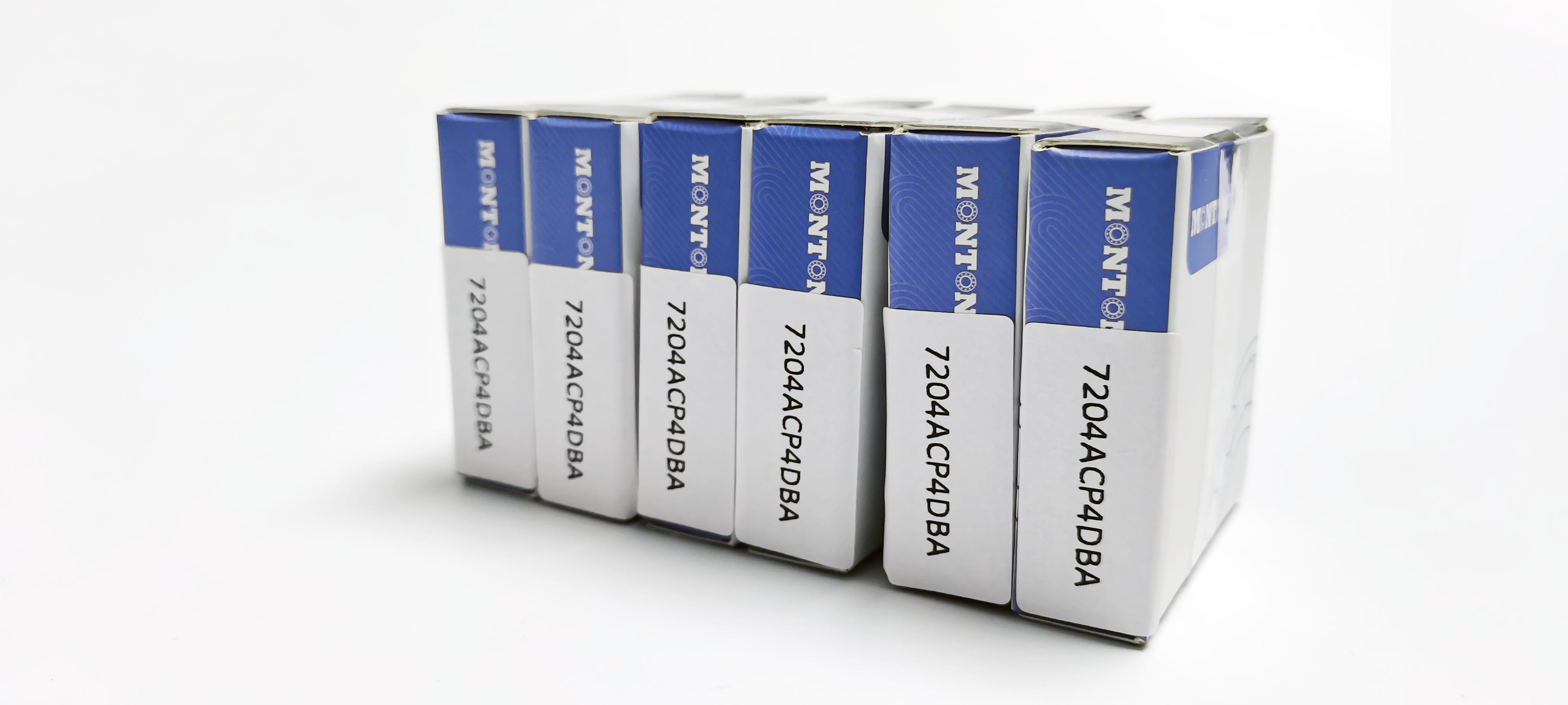
Our Quality
As a high precision bearing manufacturer, we pay highly attention to the quality of our bearings.
The tolerances for size, geometry and running accuracy of the bearings fully comply with international ISO standards
and ABEC tolerance classes.
Our bearings are filling with balls meet highest tolerance standards, ‘G5’as a minimum, and our bearings are
manufactured to P4A (P2/P4 Internal/external precision) as standard and up to P2.
We have obtiaoned ISO9001-2016 certificate,Customers can get of excellent quality and precision bearings from US.
Our products are fully traceable from the initial inquiry to the complete design and manufacturing process.
After assembly in the cleanroom,our bearings are 100% noise,vibration and quality testing to ensure that our customers always get very nice bearings for their application.
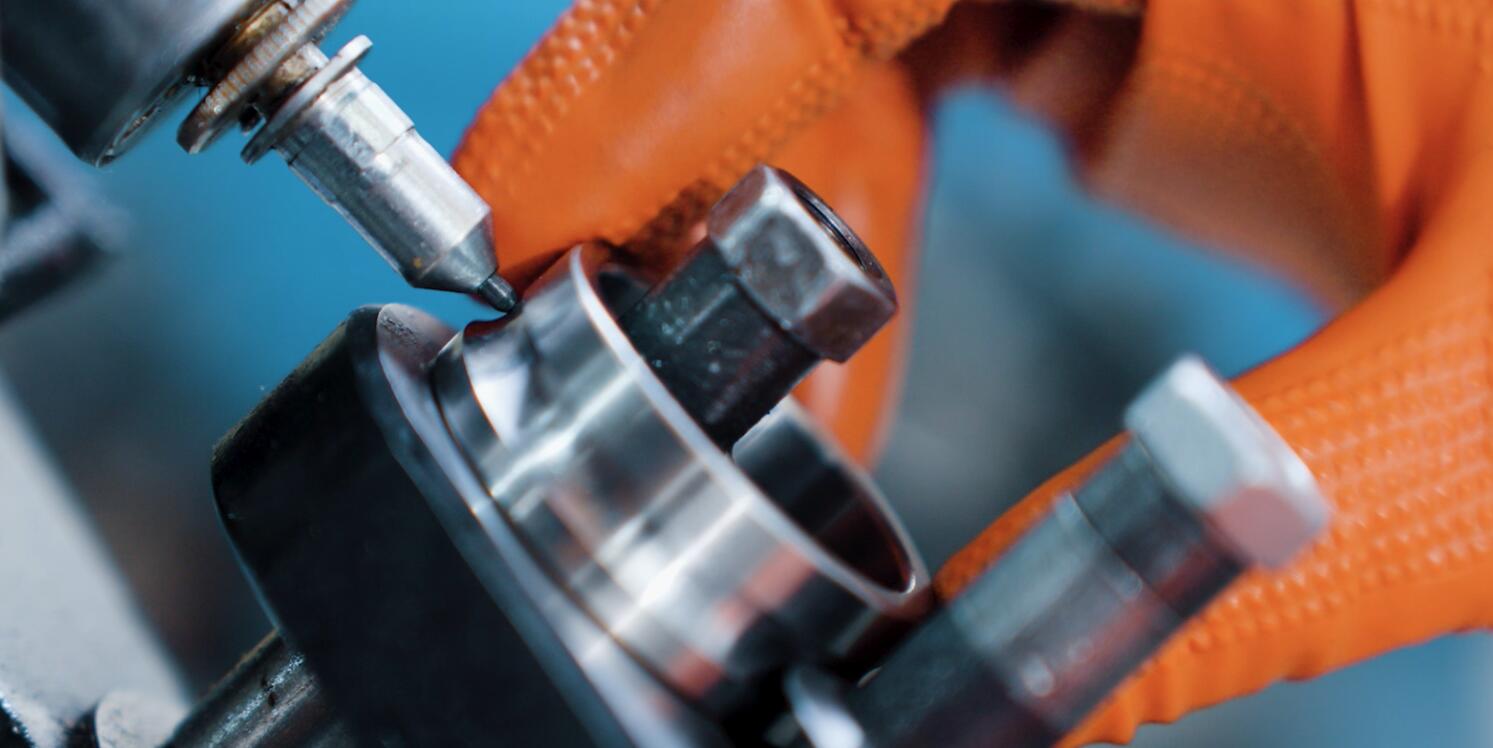
Technical support
We can not only provide high quality bearings, also offering proffesional technical support, we have laboratory and
equipment and test for bearing analysis and testing.
We also offer the following service:
1. Bearing lifetime calculations and evaluation
2.Rigidity and preload design
3.Thermal inspection
4.Shaft calculation
5.Lubricant recommendation
6.Bearing damage analysis
7.Dimensional inspection
8.Friction measurement
9.Chemical composition analysis
10.Hardness analysis
11.Micro porosity in steels analysis
12.Vibration ,Roughness,Deviations etc.
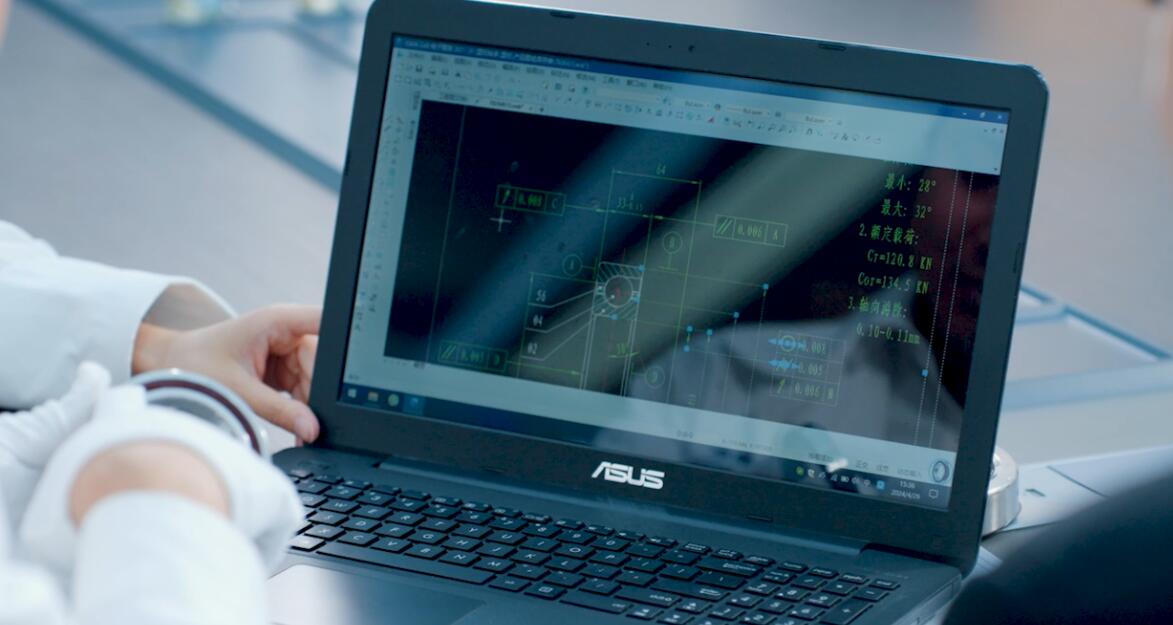
We supply bearings havewith contact angle 15˚ 18 ˚ 25˚ 30˚ or 40˚ . They can be used in pre-loaded duplex sets,
back to back (DB) or face to face (DF) for supporting thrust loads in both directions or in tandem (DT) for additional
capacity.
Contact angle is the nominal angle between the ball-torace contact line and a plane through the ball centres,
perpendicular to the bearing axis. Load is transmitted from the shaft to the inner ring and then via the contact angle
through the balls to the outer ring and subsequently the housing. To ensure an even load on all bearings within a set,
they should all have the same contact angle.
Our bearings are available with a contact angle of 15° 18° 25° 30° or 40°.
The larger the angle, the higher the axial capacity and rigidity as axial forces can be absorbed. Conversely,
bearings with a smaller contact angle have better radial capacity and rigidity and are able to operate at higher speed.
Non-standard contact angles are available on request.
Components Materials:
The parts of the bearing usually include:
1. Rings (inner ring, outer ring)
2.balls(Steel and ceramic)
3.Cage
4.Seals
5.Lubrication method
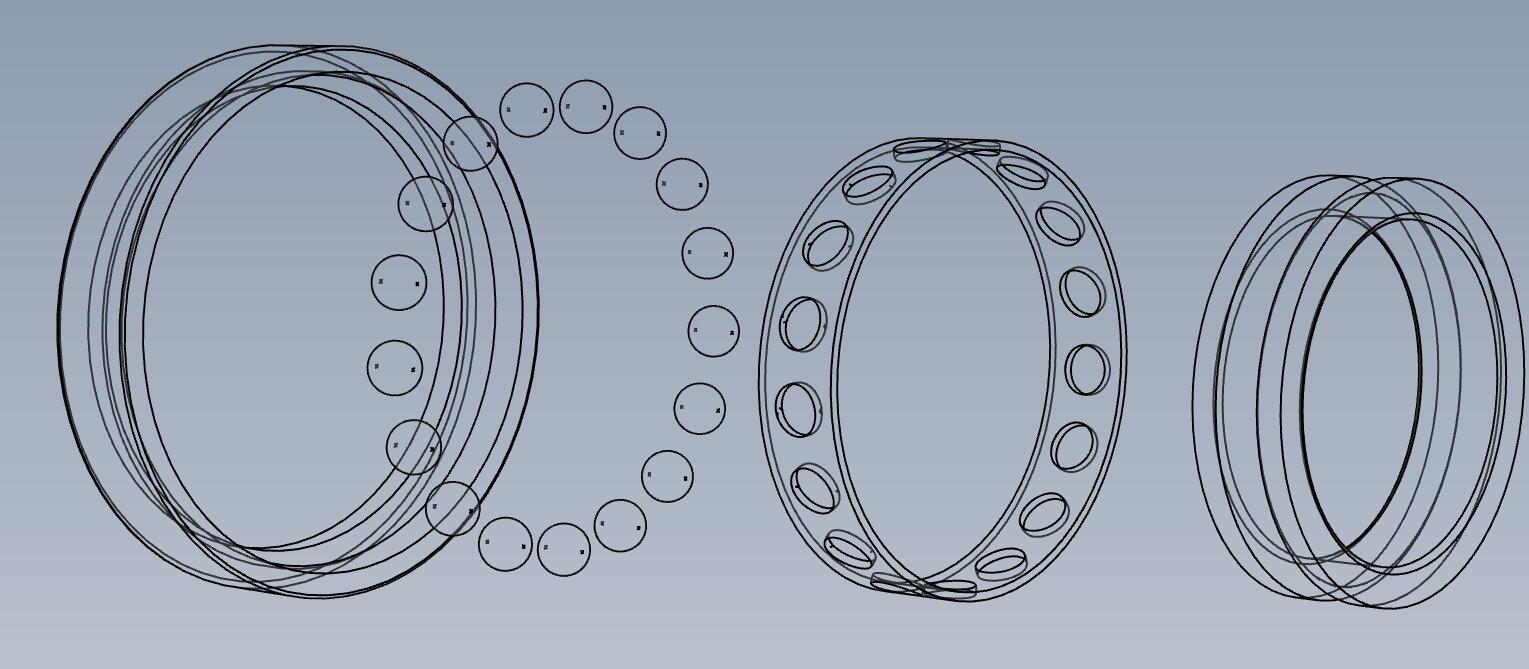
Rings:
Bearing steels such as Gcr15 (100Cr6 )and 440C or 52100 are used as standard for high precision bearings.They
have good load carrying capacity, fatigue resistance and stability.
The high-performance stainless steel material X30CrMoN15-1 can also be specified. This highly refined material
has a very fine grain structure which enhances its mechanical properties. It also provides excellent corrosion
resistance, fatigue resistance and stability.
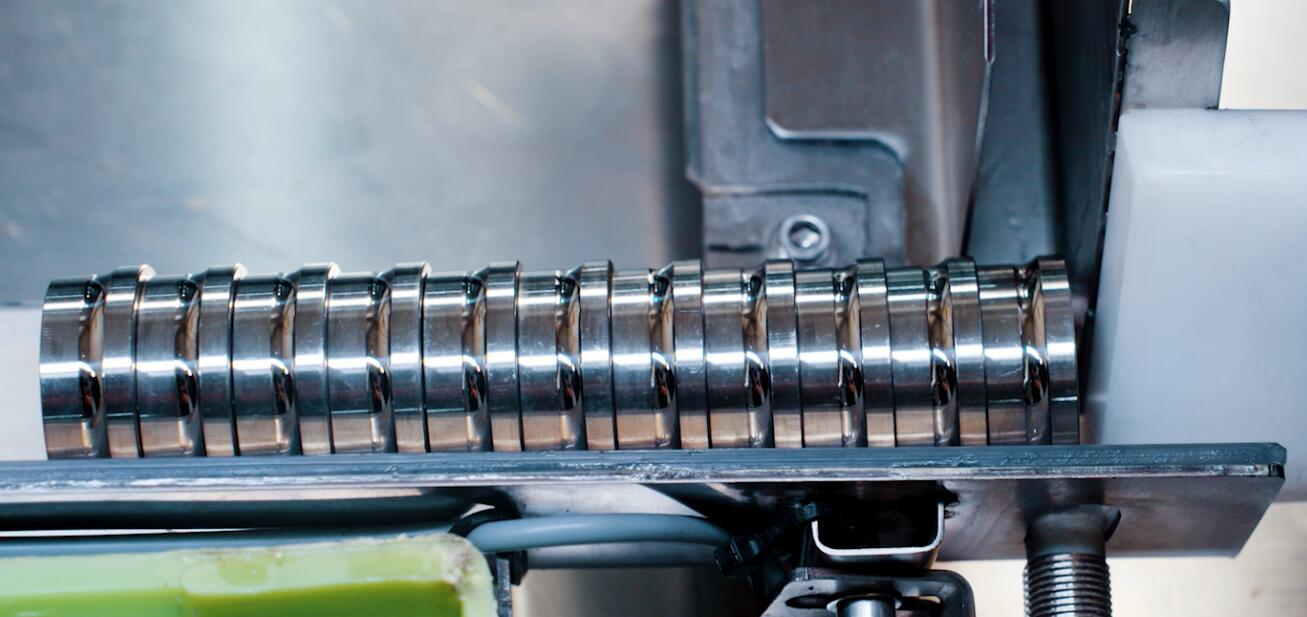
Hybrid Bearings
For special applications our bearings are filling with ceramic balls made from silicon nitride (Si3N4). Only balls of
grades 3 and 5 are used for our spindle bearings as these classes complywith the tightest tolerances in terms of size, roundness and roughness.
Hybrid spindle bearings are used to meet the requirements of particularly demanding applications.
The inner ring and outer ring are made of either carbon chrome or highly fatigue resistant X30 steel, while the balls
are ceramic (Si3N4).
Ceramic balls have several advantage:
1.Low vibration and noise
2.Highly running speed.
3.Good wear resistant and long working life.
4. Ceramic hybrids perform higher rigidity and higher natural frequency.

Cage:
Proper cage design and materials is essential to the successful performance of a precision ball bearing.
The basic purpose of a cage is to maintain uniform ball spacing, to prevent the balls contacting, thus ensuring an
even load distribution within the bearing. They can also be designed to reduce torque and minimise heat build-up.
Our cage made of fabric reinforced phenolic as standard. If required, cages can also be produced from high
performance plastics such as PEEK or Polyamide-imide . These materials are lighter, they are corrosion resistance
and low friction, in results reduced wear and less heat generation. This enables thebearings to operate at higher
speeds while prolonging grease service life.
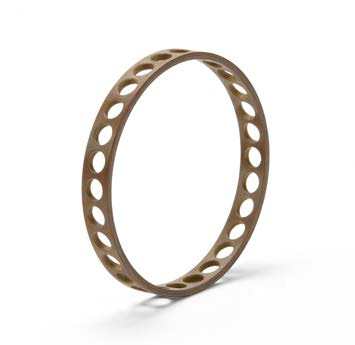 | 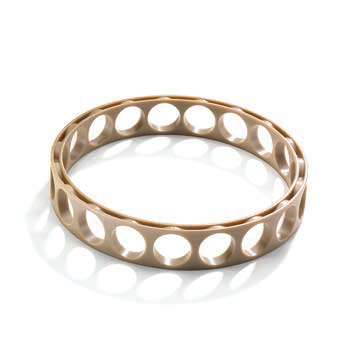 | 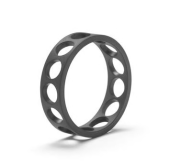 |
fabric reinforced phenolic resin cage | glass fibre reinforced PEEK cage | carbon fibre reinforced PEEK cage |
For special cages, please contact with us! |
Lubrication and Lubrication Selection
Right lubrication is very important to the performance of antifriction bearings. Increased speeds, higher temperatures,
improved accuracy and reliability requirements result in the need for reliable lubricant selection.
The lubricant is to perform an elastohydrodynamic lubricating film between the rolling element and the bearing
raceway, therefore preventing direct contact between the friction surfaces of the individual components.
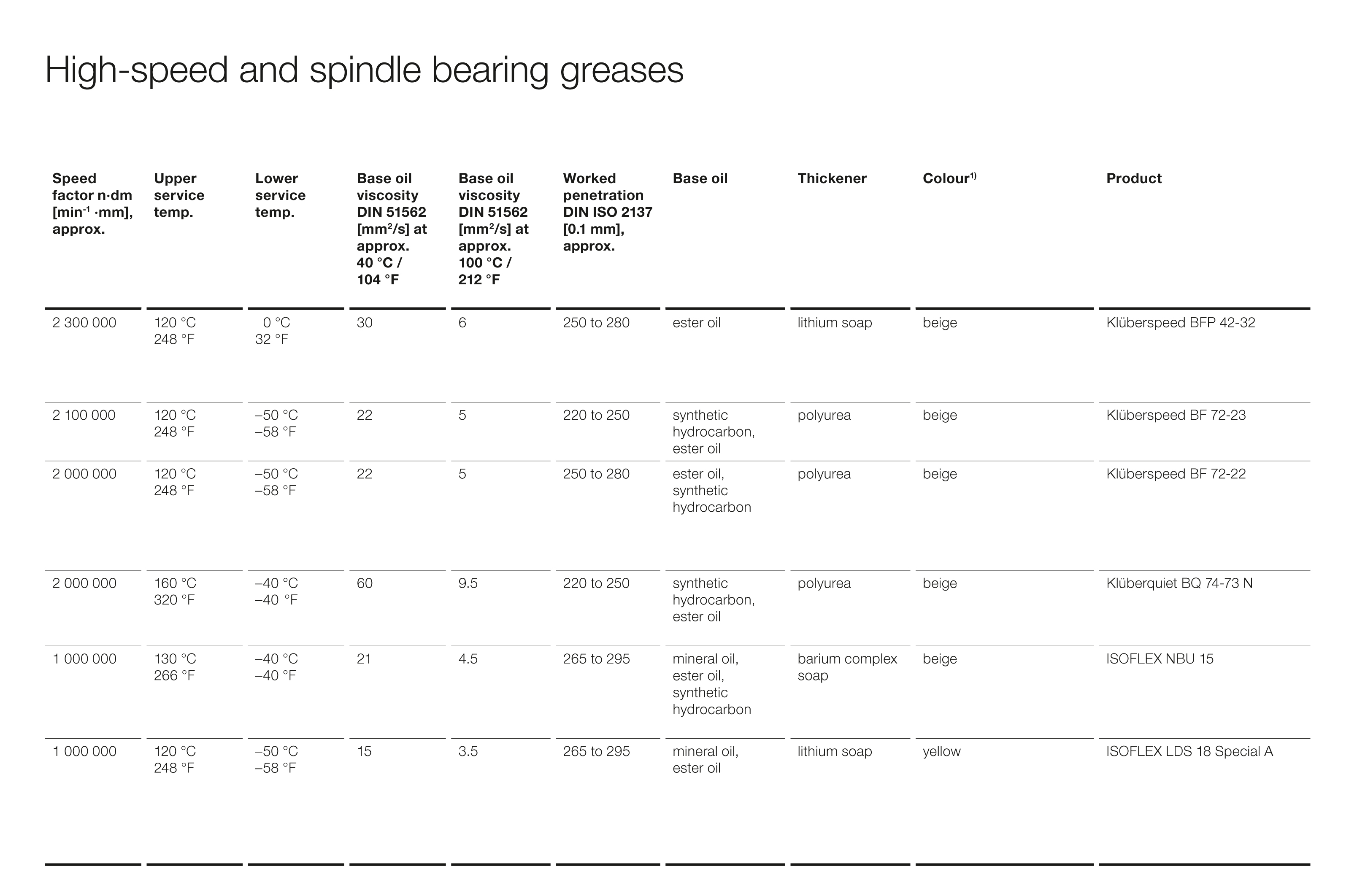
Correct lubricating film have more advantage:
1.Reduces friction
2.Reduces wear
3.Protects against corrosion
4.Dissipates heat from the bearing
5.Acts as barrier to contaminants
The lubricant type is typically selected according to the operating conditions and limitations of the application while
taking into account specific customer requirements.
The most important factors when choosing lubricant as below:
1.Viscosity of the lubricant of working temperature
2.Maximum and minimum allowable working temperature
3.Working speed
4.Required friction values
There are two kindlubricant ways: Oil and Grease, we can supply and filling grease according to your requirements.
Grease Lubrication
Advantages of Bearings with Grease Lubrication
1.Life time lubrication
2.Maintenance-free
3.No external lubrication system required
4.Optimal grease quantity
5.Use of a high-performance lubricant (speed factor n·dm = 2,200,000)
6.Greasing, sealing and packaging in a clean room Class 7

Oil Lubrication
Oil lubrication can offer more advantages compared with grease lubrication, particularly in the case of spindle
bearings rotating at high speed.
Our open spindle bearings are supplied oil lubricated as standard. In contrast to grease lubricated bearings, oil
lubricated bearings must be lubricated regularly with exactly the right amount of lubricant in order to achieve the
expected bearing life. The optimisation of relubrication intervals and lubricant quantity can have a significant
costsaving effect for the end user. If regular relubrication of the bearings is necessary, an external oil-air lubrication
system can be integrated into the system.
Oil-Air lubrication or oil minimum quantity lubrication is often used in modern machine tool spindles . In this
process, an oil film is formed in front of the spindle and conveyed to the bearing. It enables exceptionally high
speeds to be achieved and dissipates heat from the bearing.
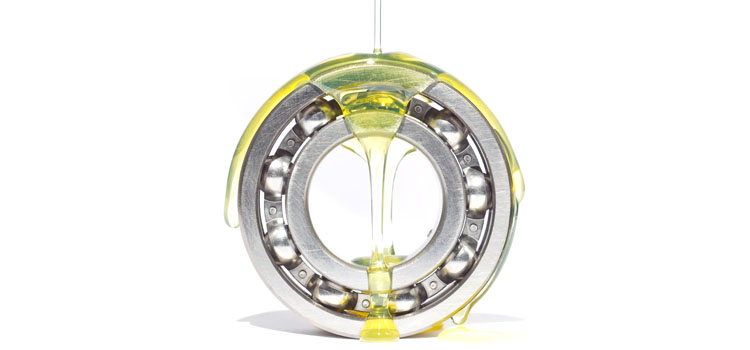
Angular contact ball bearing design
Open Design
Open spindle bearings make optimum use of the internal space by allowing large balls and a halo cage.
This results in maximum load carrying capacities and therefore maximum bearing life. This open design is
recommended for oil lubrication. Contamination should be prevented from entering the bearing and continuous
relubrication should be used.
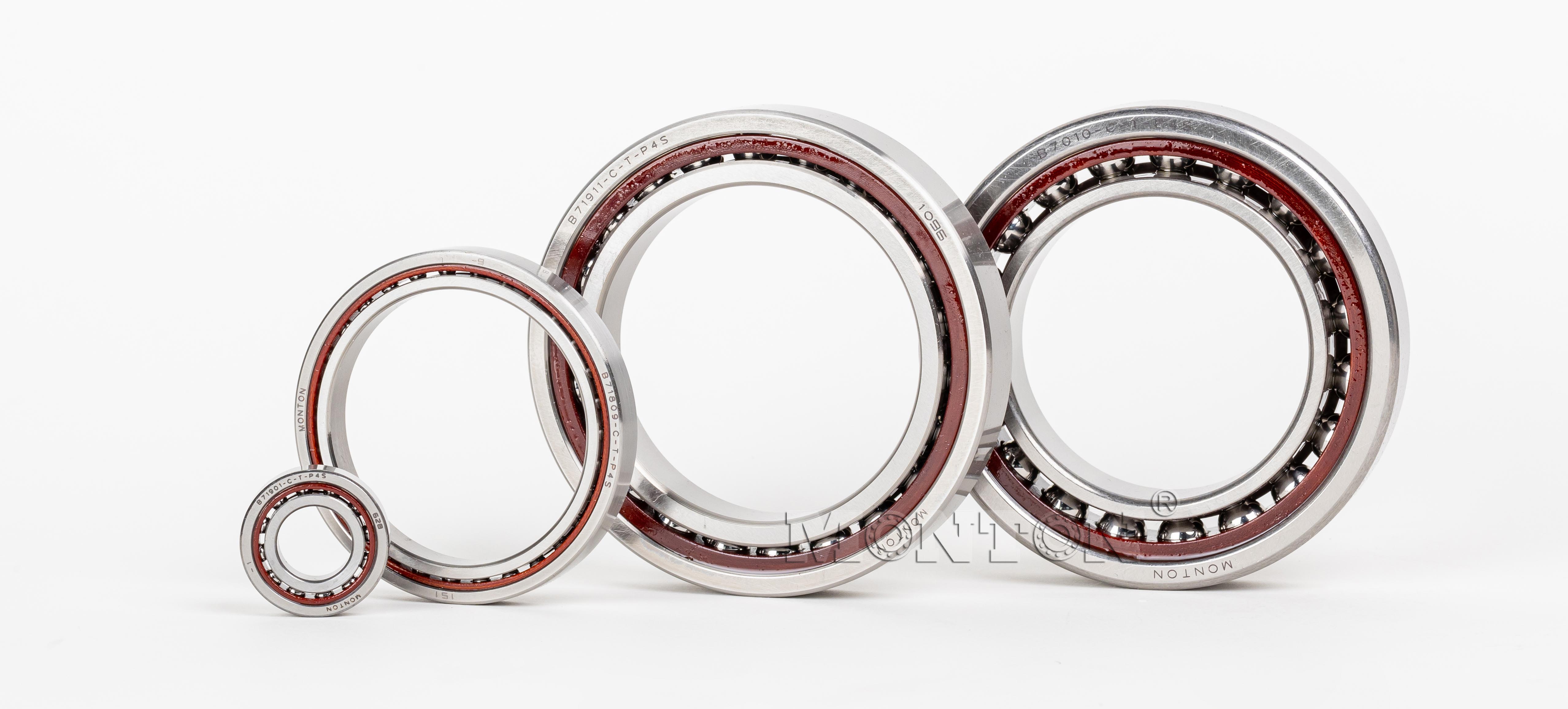
Sealed Design
Seals exclude contamination, contain lubricants, and protect the bearing from internal damage during handling.
Our sealed bearings typically have non-contact seals on both sides, which ensure good protection against
contaminants, such as dust, which could damage the internal workings of the bearing. This design also limits
lubricant leakage from the bearing. They are recommended for applications where lifetime grease lubrication
is required or where air flow through the bearing is present.
Since the seals are non-contact there is no negative effect on friction or speed ratings. Our standard seals are
made from NBR with steel reinforcement. For extreme environments the flouroelastomer is available, offering
high chemical resistance and operating temperatures up to 230ºC In some instances it is necessary to reduce
the ball diameter in order to provide space for the seals, an outcome of which can be a moderate increase in speed.
Further advantages of the sealed design include ease of handling and trouble-free installation, making it
particularly suitable where bearings are being replaced.
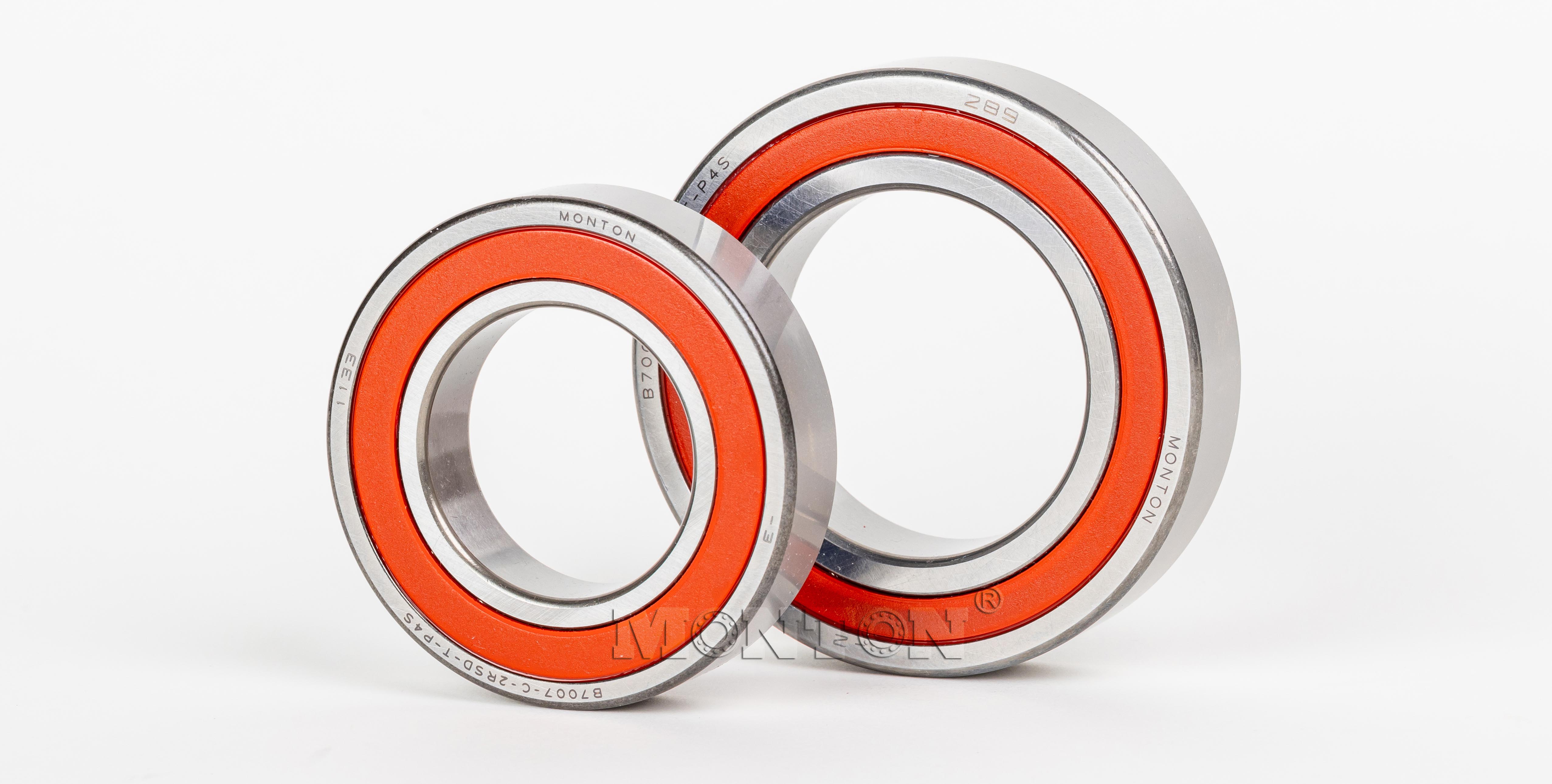
Dimension Series
70XX, 72XX ,718XX,719XX ,BNR10/19,BER10/19, BAR10/BRT10 DLR series
ceramic ball and stainless teel series etc.
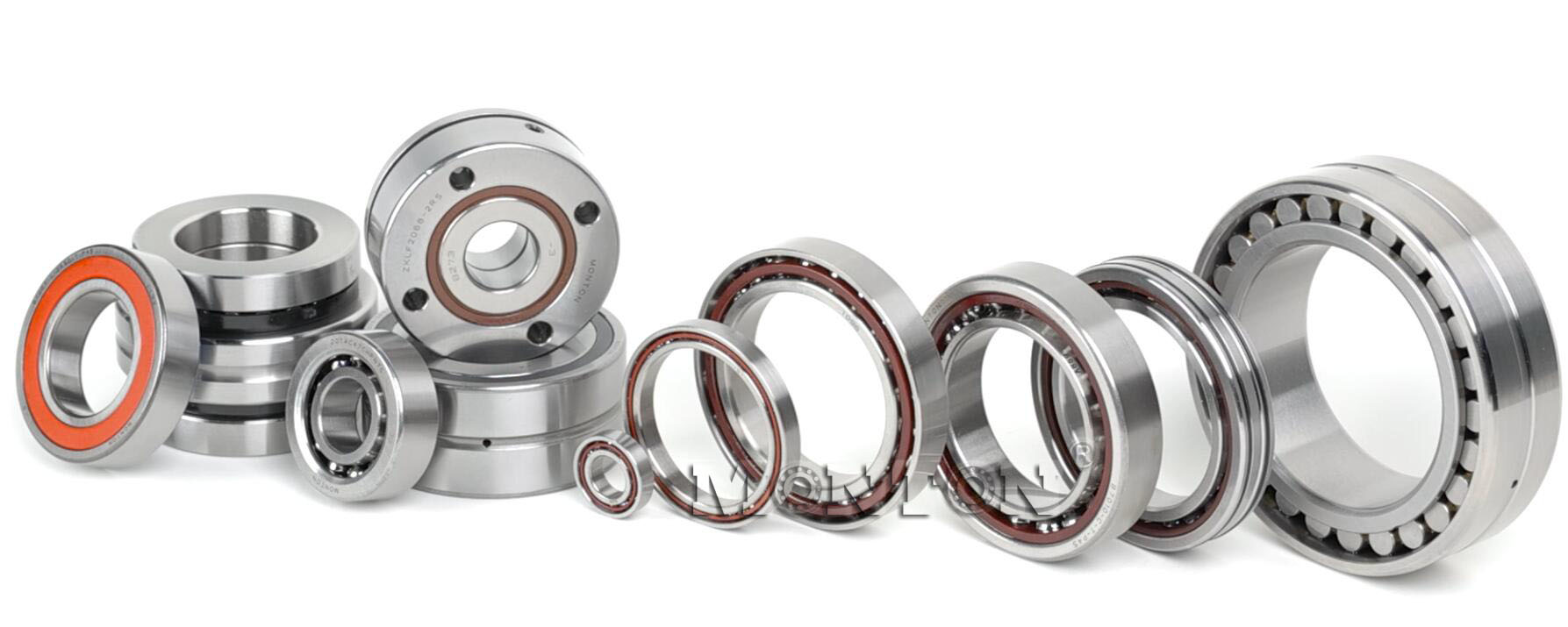
MONTON Bearing Codes

Main applications:
Machine tool spindle | Grinding motor spindles | Motorised spindles |
Belt driven | Mechanical spindles | Rotary unions spindles |
Linear transmission | Machine tool workpiece shaft | High speed electric shaft |
Planetary reducer | Drill head shaft | Servo motor |
Aerospace | Unmanned Aerial Vehicle | automobile |
We warmly welcome all friends come to visit us, study or business negotiation.